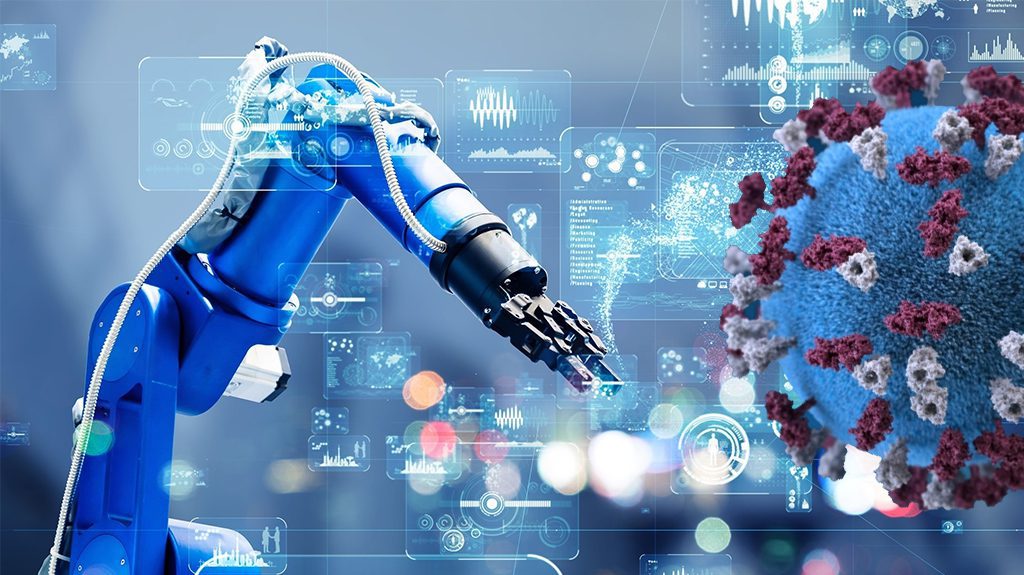
The environment in which electronics manufacturers are building has changed rapidly in the last couple of months. As under-resourced teams face the challenge of solving COVID-19 problems, they’ll need technology that gets to the very root of these issues: solving for distance. Between solutions that leverage the power of the cloud for visibility and automation that optimizes work, necessity will drive invention: manufacturers will do five years of innovation in the next 18 months.
Adoption of cloud data will unlock remote oversight, remote work, and optimization
Cloud databases are uniquely suited to help manufacturers aggregate data across multiple on-premises systems, something that enables reduced travel and distance during COVID-19. To date, the manufacturing industry has lagged behind in the adoption of cloud technologies – favoring on-premises solutions as the “safer” place for sensitive manufacturing information. Despite lingering unfounded security concerns, the benefits of the cloud have become too good to ignore and even before COVID-19 mindsets had started to shift. By aggregating their data in the cloud, companies get real-time data for remote oversight, aggregated and comparative intelligence across global factories, suppliers, and business units, and the ability to leverage technologies to solve pressing problems. Adoption of cloud data unlocks technologies like AI, which can be used to surface unanticipated defects during development and catch quality shifts in production without stepping foot in the factory. Implementing cloud data should be a top priority for both manufacturers and the brands that build at them. In the short term this data enables some level of oversight and normalcy in a world where engineers cannot travel, and in the long term it will pay dividends for manufacturing optimization of products and processes.
Automation has an unprecedented opportunity
Electronics manufacturing is a highly manual process. Hundreds of pairs of hands touch phones and laptops during assembly. These products are developed, ramped, and run over months, not years – investment in automation for products with such short cycles doesn’t pay off. Line space is at a premium, so before COVID human operators were placed at 0.6m intervals – that spacing will need to be significantly increased in order to meet guidelines to reduce virus transmission. Couple the spacing issues with PPE requirements, and the increased cost to keep human assembly safe creates an unprecedented opportunity for stronger returns on investment for automation. While manufacturers may initially be hesitant to take on large capital intensive projects like automation right now, the payoffs of a workforce that doesn’t take breaks and doesn’t get sick will be appealing to those with strong capital positions – enabling acceleration in efficiency during this time that will cut costs and boost bottom lines.
Necessity will drive adoption first, then more innovation
If you talk to folks in the manufacturing industry, you’ll find that many have been burned by falling for the promises of buzzwords over the past decade. This has left a general aura of suspicion around new technologies for leveling up – though technology investment in manufacturing remains high when there is a pressing need. Today’s need is great – manufacturers will be looking for solutions that directly solve their pain points, can be implemented quickly (days and weeks, not months), and have the potential for long-term, post-COVID-19 impact.
COVID-19 requires the modernization of manufacturing. Since the problem of “distance” can’t be solved without the adoption of technology, we’re going to see many years worth of innovation in the next 18 months. Many of these solutions will bring greater efficiency, lower costs, and less waste, enabling them to outlast the pandemic and pay for themselves quickly.
Experience years of innovation manufacturing in mexico.
Source: Forbes
https://www.forbes.com
US toll-free: +1 (877) 698 3905
CAN toll-free: +1 (844) 422 4922
start@americanindustriesgroup.com
Please note that we do not accept job applications here. If you are interested in applying for a position, please visit the following link: https://www.americanindustriesgroup.com/jobs/